We recently had the opportunity to talk to Krzysztof Wróblewski , CEO of Polish pyrolysis operator Contec. Wróblewski is keen to sell his ideas on recycling and pyrolysis and Tyre and Rubber Recycling has the unabridged interview in Podcast 37 for those looking for more information on the project.
TRR: The first question I have for you Krysztoff is, can you give me some background to the business itself? What exactly is Contec?
KW: Contec is technological company covering a pretty wide spectrum because we started from R&D, moving onto the design and building construction and starting up our first pilot plant. Over the last couple of years, we have been operating the plant and perfecting the technology. Today, we are running at almost full capacity. Now, we want to bring our technology to the market and operate multiple plants.
TRR: Okay, so you have developed molten salt bed technology. Do you have the equipment built in Europe to your specifications?
KW: We have designed and built the plant in Szczecin near the German border. It has not been easy, but throughout the years, we managed to stabilise the technology, and now it is working really well, and we want to scale the process.
TRR: You mention scale, what sort of capacity does the plant have today?
KW: Currently we are processing over 1000kg per hour. If we worked throughout the year at 100 per cent, we would reach something around 10,000 tons, and this is small from one point of view and big from the other – big because it is not a laboratory scale.
However, it is too small to have the capacity that will allow for a significant impact on sustainability. Our vision is to accelerate the transformation of the manufacturing industry into circularity. Right now, the demonstration plant is too small. That is why we want to start the expansion project of the Szczecin plant, which will allow us to more than double our capacity in Poland, and also in 2024, we plan for several new plants.
TRR: Are you looking at developing these new projects in partnership as joint ventures? Are you looking to license them? Or are you looking to try and maintain control of the process?
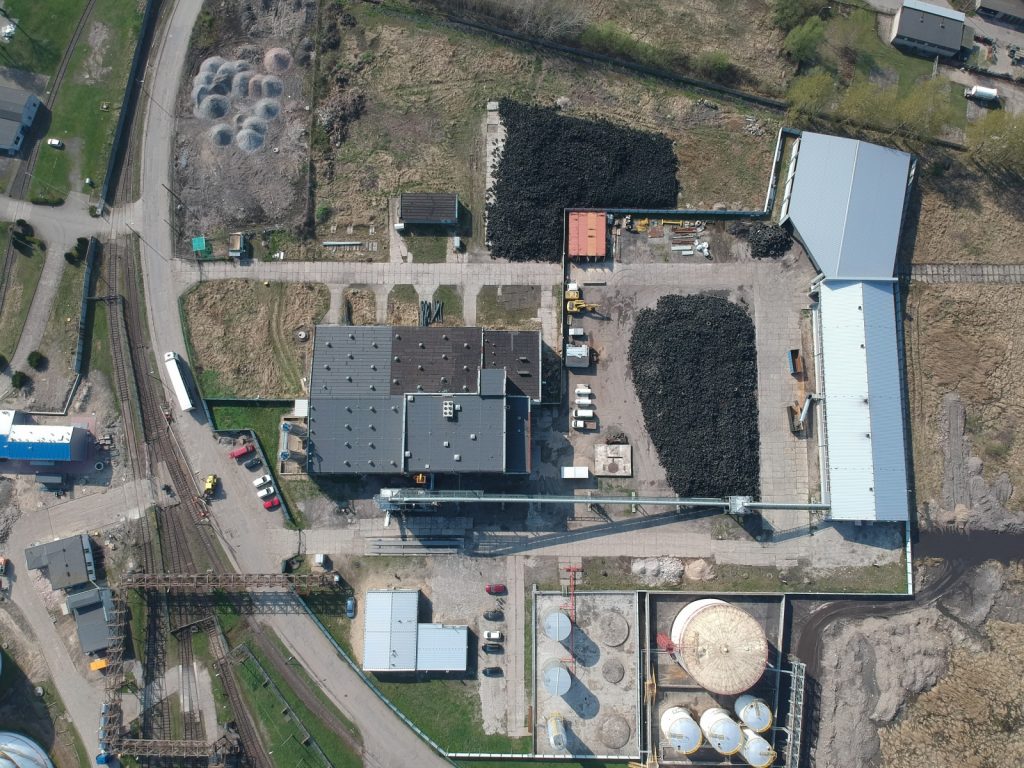
KW: We are not going to be a technology seller or provider; we believe that our technology is really good, but we put a lot of R&D and effort into stabilising the technology. We have the know-how, and we want to control it.
That is why we want to be the sole operator of the plants. Of course, there might be joint ventures with several players, we are already in talks with one.
The typical plant that we want to build would be with a nominal capacity of around 40,000 tons of ELT because we believe that dispersion of the plants can shorten the supply chains and take care of local end-of-life tyres, instead of building one or two mega factories.
TRR: In reference to markets, a lot of people in the pyrolysis business have focused on the tyre industry. That has proven to be quite difficult until recently. What are your thoughts on that sector of the market?
KW: I think that there are three main problems, and the first was the lack availability of really good rCB finishing clients. Only recently have we seen the finishing equipment from companies like Mars Minerals; they did really good R&D and built product lines, especially finishers for rCB. I think the availability of quality rCB finishing equipment will bring higher finishing qualities for rCB.
I think the second part is what is in the middle of the process itself. Because to have something good for the finishing client, you have to have really good, solid repeatable rCB with consistent quality and also the oil from the process.
You can only achieve that with equipment that is stable and runs smoothly. I do not want to market our technology because there are lots of technologies out there, and a couple of them are running really nicely, but here comes our molten salt bed, which stabilises the temperatures throughout the reactors. Our reactors control residence time distribution. This is what you need to have a stable, reliable and repeatable quality of the rCB for best-in-class black. The third problem is the feedstock control.
As players we have to take the kind of feedstock that we get from the market, but we have to control it somehow, because we have different in-rubber performance of rCB which is made only with passenger car tyres. But we have quite a different rCB from truck tyres. This was discussed when Michelin and Bridgestone showed their white paper. I think it is particularly important for the industry to hear voices from the leaders of the tyre manufacturing industry, because they said in this white paper that they think that the best solution for the pyrolysis industry to grow to produce sustainable and superior quality rCB is to pyrolyse 80% to 20% of the car tyres in relation to truck and bus tyres. So, this has to be included in the process. With these three things resolved, I think it is possible to get the rCB into the tyre industry, especially in the carcass and the sidewall instead of some 660 grade virgin carbon blacks.
TRR: If we talk about the feedstock, is it important to remove tread, or have feedstock that has minimal tread on it?
KW: I mentioned that recovered Carbon Black could be incorporated into carcasses and sidewalls. But what we want to pyrolyse is the tread because in the tread there are the best reinforcing virgin carbon blacks, especially in truck tyres. We also consider that the composition of the tyres is changing from year to year.
I understand that everybody from the rubber and tyre industry would like to have a very stable, rCB with every parameter as stable as possible, but the feedstock is also changing. And we have to talk about that with everyone. Right now, the ash content is lower, but we can see that in the future, the ash content will be higher.
TRR: You essentially have a dynamic feedstock in that the tyre manufacturer is constantly changing the compounding. So, you do not know what you are getting until you have it.
KW: To some extent, I think this is a problem that is overcome maybe if you just switch to one manufacturer’s waste – that would be more stable. To be honest, I think that everybody will have to tackle it and the industry will have to solve it because there is also the emerging market of electromobility. The tyres are different as you might imagine. So, the recycling of these tyres will be also a bit different than the products that we have right now.
TRR: I think the single supplier, the single manufacturer is possibly a route that might have to be taken. We see Michelin in Chile recycling their own tyres, because they know what is in them and what they can do with them. If you are processing tyres from multiple manufacturers, particularly in that sort of volume, you have no idea of what you are getting until you have it.
KW: But we have to solve the problem, don’t we? So, we have to tackle it and the answer for that is also scale, because if you produce just 300 or 3000 tons of rCB you have these vulnerabilities in the composition, but if you have several plants and you can blend all the rCB together, you can create useable rCB, which will have better stability and quality, but this only can come at scale.
TRR: So, volume gives you stability. I understand that the virgin carbon black market has similar issues, and the tyre manufacturers know that carbon black that comes from plant A will not be the same as the carbon black that comes from plant B from the same company. They adjust the compounding to suit what was coming in. I am sure that they can do the same with recovered carbon black.
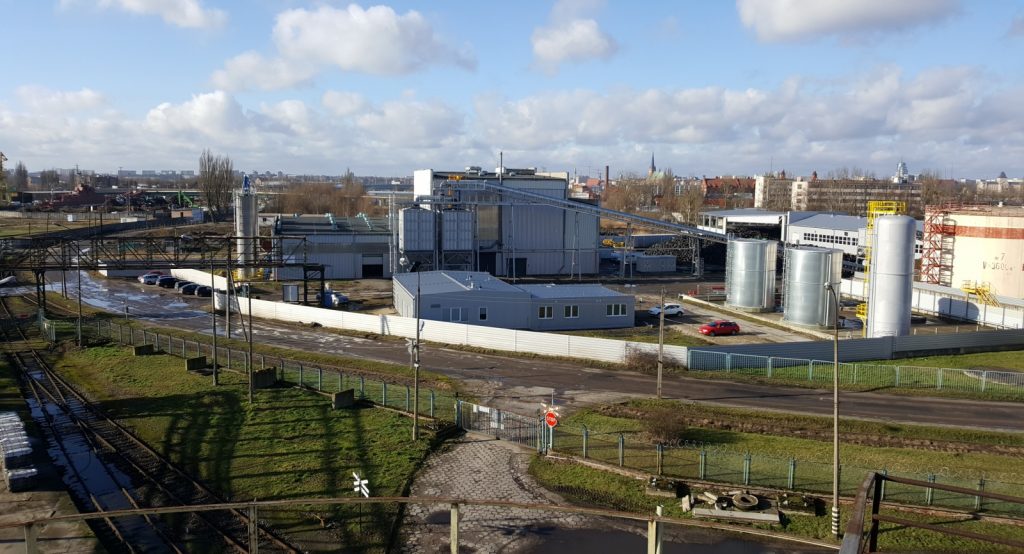
KW: I think for the tyre manufacturers there is a bigger difference than if you have the change from N660 from one producer to another producer, than if you have a plan of 10% of rCB in the previous standard mix. I think that you are right that the engineers have to have to work hard with us, but the thing that is especially important in this industry is collaboration, that we are open to talk with different players, that we are open to sharing the results because we need some degree of transparency.
Because the rCB will be something that can be used in rubber, we have to control the feedstock. We have to have a really good finishing client to mill below 15 or even 10 microns, and we have to pelletise the rCB, and that is why we decided to go with the best-in-class Mars Mineral pelletiser.
I think there are certain steps that are being treated as a golden standard right now, and the transparency and collaboration with all the companies involved in the supply chain is what will bring the rCB to the scale that might be used in tyres and the tyre pyrolysis oil (TPO) to a quality that is acceptable to refineries and chemical companies for reprocessing.
Our way of thinking about the TPO is to get it into the tyre manufacturing ecosystem to be true tyre-to-tyre recycling, and I am really impressed by companies such as Orion trying to produce sustainable carbon blacks with the use of TPO. I think it is great direction because this is a material content tyre to tyre recycling.
If we turn it into energy, the TPO has a unique composition. It has lots of aromatics and lots of bio content, and I think it would be really good to be used in some industries, for example, BASF. That company stated that it wanted to buy 150 kilotons per annum of TPO in 2025. And that is a strong call for the industry to scale up quickly because there is demand. With these public declarations, as the CEO and CTO of Contec, I have an easier time in convincing potential investors.
TRR: To build these larger plants, you need considerable investment. In the UK, we see some companies coming forward looking to build 50,000 ton plants. One of the barriers that they face is that there is a lack of security of feedstock. So, in the UK, it is particularly bad because we ship 200,000 tons of tyres a year out to India, possibly Turkey. Even in Pyrum’s annual report they listed the risk to the company through lack of feedstock through exporting. Is that likely to be an issue for Contec?
KW: Nobody is immune to that. But if you create value with the technology, and if your products are really substantial value, these are the major revenue streams for the power of this company. So, what I am going to say is that even if we had to fight for the tyres, if we have the technology which delivers superior quality, the tyres are not a relevant part of the stream. Right now, we are getting paid, of course for taking the tyres, and these amounts are really good. But even if the tyres were free, this is still a sustainable business with remarkably high margins.
TRR: One last basic question. Do you process shredded tyres or whole tyres?
KW: We bring whole tyres into the plant because we want to control the feedstock. We want to see what we shred. We have our own shredding equipment, and we tried to buy the best in class The shredding system is Columbus McKinnon, and we have been using it for a couple of years. We produce our own steel and rubber chips below 25 millimetres.