Zeppelin Systems and RCB Nanotechnologies to offer a solution for cleaning recovered carbon black.
Scrap tyres go through numerous recycling processes before they become new tyres. However, there is a distinction between material recycling, raw material recycling and chemical recycling as the final finishing step of pyrolysis worldwide.
As an integrated solution provider with over 40 years of experience in the tyre industry, Zeppelin Systems collaborates with international partners in all aspects of scrap tyre recycling.
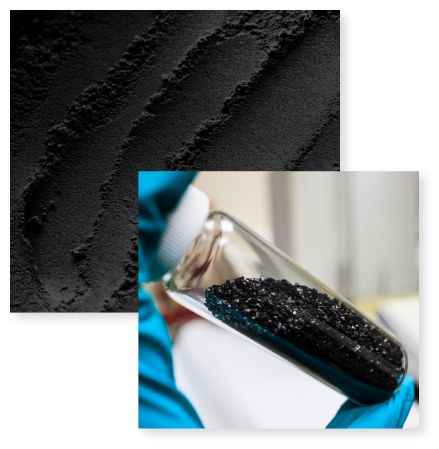
The German company RCB Nanotechnologies specialises in the finishing of raw-recovered carbon black. The company thus perfectly complements Zeppelin Systems‘ wide range of services throughout the sustainable circular economy for the tyre industry.
Carbon black is found in almost every black rubber or plastic product. A large part of the high-tech industrial material produced – around 70 per cent of worldwide production – is required to make tyres. To produce one ton of carbon black, manufacturers use approximately 1.5 tons of fossil raw materials as well as large quantities of water. In addition, the carbon black manufacturing process generates up to three tons of CO2 emissions.
It is estimated that there are currently around four billion scrap tyres in landfills worldwide, and one used passenger car tyre contains around three kilograms of carbon black. However, thanks to innovative technologies for chemically treating scrap tyres, this previously unused material could be recycled much better in the future.
“There is promising potential for customers and the environment in the industry-wide recovery of carbon black,” says Dr Markus Vöge, CEO of Zeppelin Systems GmbH.
“We want to offer our customers sustainable alternatives for tyre production – with consistent quality and in sufficient quantity,” adds Guido Veit, Vice President of Sales for Polyolefins, Rubber and Silos at Zeppelin Systems GmbH. This is precisely where the Friedrichshafen-based system engineering company and RCB Nanotechnologies step in.
RCB Nanotechnologies developed a revolutionary process in collaboration with the Fraunhofer Institute for Building Physics IBP. In this process, the ash content (up to 25 per cent) is separated from the raw recovered carbon black obtained by pyrolysis. The results are a high-quality and extremely pure recovered Carbon Black (rCB).
Numerous tests with well-known tyre manufacturers confirmed that the rCB quality is comparable to the original industrial material (conventional Carbon Black, for example, N660 or N772). Thus, certain standard Carbon Black grades can be 100 per cent substituted in the future. In addition, other high-quality products are obtained in the process, such as silicon- or zinc-based compounds. This creates further sustainable material cycles in the construction and tyre industry process. Zeppelin Systems can easily integrate RCB Nanotechnologies technology into existing and new pyrolysis plants as a solution provider and system integrator. As an engineering and implementation partner, Zeppelin Systems uses its many years of experience to create solutions for the challenges of its customers daily.