One way to use the ground tyre rubber (GTR) is to add it to the rubber compound. As a filler, GTR has a potential to blend with virgin stock. The highly crosslinked nature of the GTR inhibits any molecular diffusion across the interface. The macro-sized GTR raises the viscosity and reduces the workability of a virgin rubber compound. Usually, utilising GTR independently of size results in worse rubber mix integrity and gradual decline in basic physical properties which lead to detrimental changes of the key technical parameters.
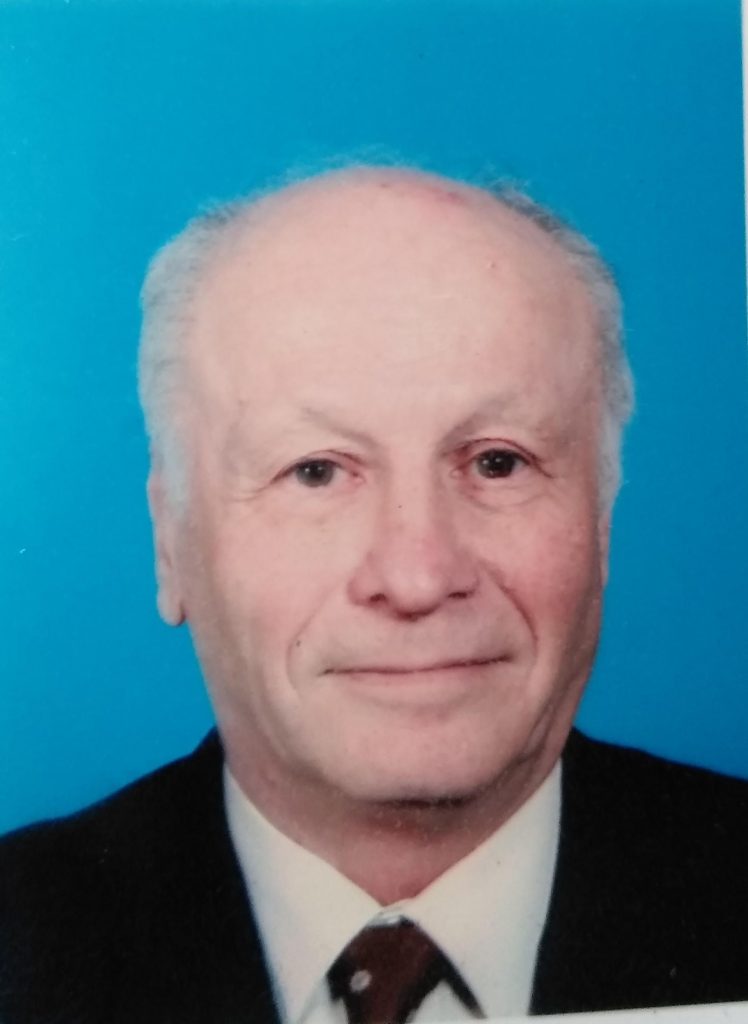
Moshe Rakhman Identifies New Route to Production
The current method of GTR incorporation is based on GTR thermo-mechanical surface activation at the first compounding step that assists with technological compatibility. Due to crosslink networks, GTR aggregates are not typically broken under the normal mixing shear.
When a large amount of GTR is blended the cavities formated have a negative effect on the non-uniform distribution and mix fluidity. At the same time, Mooney viscosity and minimum of the MDR curve are increased [1]. This is expressed in a rough surface skin effect.
The use of GTR in elastomer compounds has a number of limitations – viscosity and roughness are raised, adhesion is reduced, fatigue properties are adversely affected. Excluding the rubber trimmings generated prior to the final heating and curing of new tyres, it is estimated that less than 0.1% by weight of all ELT are reincorporated into a new tyre master batch.
Reuse of GTR in high performance products is limited to exceedingly small quantities (with no more than 3-5% being the limit added) because the GTR typically adversely affects key properties vital to the performance.
Functional processing of the GTR/Elastomer unvulcanised masterbatches is hindered because of the surface defects, building tack, and green strength.
Durability of a GTR-containing elastomer formulation, such as fatigue life and wear resistance, are affected substantially by macro-dispersion quality. The compatibilisation strategy is focusing on applications such as the recycling of tyres of different origin, as well as the development of new materials based on plastic/elastomer blends. The aim of the research is the development of process knowledge and recommendations for the GTR conversion in an internal mixer.
The Rubber-Functionalised Promoter
The development of a rubber-functionalising promoter for conversion of an immiscible phase-segregated GTR into a tacky-malleable, re-compoundable and re-cured rubber macro-composite is the chief aim of this current study.
The promoter should accelerate an oxidative desulfurisation (ODS) and targeted scission of sulfidic crosslinks to start at lower temperatures. With this aim, a rubber-functionalised promoter has been based on a polyoxometalate (POM) formed by the condensation of metallic oxyanions (Mizuno et al, 1997) [2], that provides an oxidative desulfurisation and a conversion of a GTR into integral macro-composite at specific blending parameters such as mixing time, initial mixing temperature and fill factor.
Two compounding tools for conversion GTR into rubber macro-composite use the promoter were used:
The first tool uses a promoter to obtain masterbatch with enhancing processing and mechanical properties;
The second tool – incorporation of nonpolar GTR in virgin rubber compound.
We report a facile strategy for combination of GTR with immiscible elastomers, comprising carbon black (CB), curatives, and antioxidants to provide workability and durability.
The GTR problem relates to poor macro-dispersion where three major categories can be defined: dispersion efficiency, surface defects and product performance. The present study therefore includes no detailed examination of this aspect; instead, the effect of the type of modification will be compared and interpreted.
Influence of Promoter on GTR Compatibilization and Macro-Composite Properties
The relationship between elastic macrogel dispersion, and crack growth propagation is expressed in viscosity of uncured mix. A rubber macro-composite with elastic macrogels are capable of satisfying a predetermined hardness, tensile, elongation, and abrasion loss as well as reducing standard deviation for stress-strain properties.
In the composition with promoter, the viscosity and viscous torque were reduced, better surface tack and green strength were observed. The resulting TyrElast compound presents a homogenous rubber blend where the process preserves the original microstructure of the rubber and allows it to maintain a relatively high molecular weight. TyrElast meets or surpasses the performance requirements for a broad range of consumer and industrial products. The TyreElast has an original rubber smell. Composition and properties are presented in Table 1.
Table 1– First compounding tool – TyrElast composition and properties
Formulation | Reference | With promoter |
TyrElast based GTR 40 mesh | 100 | 100 |
Polymer/oligomer/oil | 50 | 50 |
Curatives (ZnO, S, accelerators) | 7 | 7 |
Promoter | 2 | |
Processing properties | ||
Viscosity ML(1+4) at 100oC | 78 | 53 |
MDR at 143/40′, TS2, min | 3.6 | 3.7 |
TC 90, min | 7.7 | 6.8 |
Mechanical properties | ||
100% Modulus, MPa | 1.9 | 1.7 |
Stress at break, MPa | 6.9 | 11.4 |
Elongation at break, % | 286 | 359 |
Tear Die C, kN/m | 18 | 27 |
Standard Deviation, % | 22 | 4 |
From the obtained results, TyrElast reduces bulk viscosity, enhances properties and standard deviation.
There was no significant role of the Promoter presence on cure characteristics or scorch and cure times
TyrElast is new compound for full or partial virgin rubber substitution in all ratios. Advantage – desulfurisation during the mixing cycle; Disadvantage – two-phase mixing necessary to add in final step reinforcing filler, processing oil, and curatives. TyrElast rubber masterbatch containing modified rubber, carbon black and oil, consists of up to 50% hydrocarbon rubber. It should be used “as is” and can replace up to 100% of natural/synthetic rubber for industrial medium-value products. TyrElast benefits are in Table 2.
During mechanical mixing, domains of the lower viscosity material deform and encapsulate the thermoset phase to produce a “globular” morphology [4]. Generally, alteration of the independently controlled mixing parameters of the internal mixer such as mixing time, rotor speed, initial mixing temperature and fill factor significantly influence the GTR dispersion (or ‘‘state-of-mix’’) [5]..
The above process allows using a greater ratio of GTR and cancels the rubber reclaiming stage prior to compounding with virgin rubber for similar performance retention. The technical result results in a certain processing viscosity minimum level of rubber macro-composite.
Optimisation of the process requires balancing competing factors: exact reaction temperature and duration. The ratio of added chemicals depends on the GTR origin, molten matrix type, and the filling factor. The final step is subsequently incorporating curatives and kneading up to temperature of less than 110°C. The solubility of both sulfur and accelerator while vulcanising is different in the phases and elastic microgels, because the virgin rubber initially crosslinks more rapidly than modified GTR. Depending on the intended use, the additives mentioned above are selected and commonly used in conventional amounts.
TyrElast consists of up to 50% hydrocarbon rubber It should be used “as is” and can replace up to 100% of natural/synthetic rubber for industrial medium-value products. TyrElast benefits are in Table 2.
Table 2 – TyrElast Benefits
Masterbatch feature | Potential Performance Benefits |
Workability | Retention of dispersion of fillers and other components, stick/release to roll mill, building tack and green strength retention. |
Durability – wear and fatigue | Abrasion resistance
Crack resistance |
Tire | Grip, dry and wet traction |
TyrElast is added to compounds that should be used in advanced products, including tyres, industrial rubber, and construction materials. TyrElast is an eco-friendly material with low processing cost with its function to substitute for conventional virgin rubber.
Second Tool – GTR Direct Incorporation in Virgin Elastomer
The GTR was produced by Tyrec Ltd by ambient process. In this investigation, ground rubber was used size 40 mesh (below 425 microns) from truck tread buffing TR-40B and from whole truck tyre TR-40TK.
All compounds were mixed in an internal mixer with 1.5 l volume at a fill factor of 75 %. The temperature of the kneader at the beginning of the mixing process was 60C. Straight after the mixing process, the batch was put on the mill at 60 °C for defined cooling with friction 1.4. Afterwards, the crosslinking agents were incorporated in the internal mixer for 3 min with the same settings above. Rubber masterbatch was homogenised with friction 1.4, after- without friction and a gap of 3.0 mm; deposition of the batch. Compositions comprising GTR and promoter are presented in Table 3.
Table 3 – Composition with GTR direct addition, phr
Components | Control | GTR+elastomer | GTR+elastomer+ promoter |
Elastomer | 100 | 100 | 100 |
GTR 40 mesh | 20 | 20 | |
Carbon Black | 50 | 50 | 50 |
Processing oil, aids, resins | 20 | 20 | 20 |
Antiozonants | 5 | 5 | 5 |
Curatives | 7.5 | 7.5 | 7.5 |
Promoter | 2.5 |
A carbon black high surface energy hinders interaction of GTR with chemicals and elastomer. The batched sample in absence of a promoter shows a higher viscosity and crack propagation rates (tear) and standard deviation due to a worse dispersion and compatibility of the GTR with virgin rubber. The use of a promoter lowers the viscosity in comparison with the GTR+ elastomer are presented in Table 4.
Table 4 – Processing and mechanical properties of the tire formulations with Direct GTR incorporation
Control | GTR+elastomer | GTR+elastomer+ promoter | |
Money viscosity 100C(1+4) | 65 | 81 | 62 |
MDR 143C@35min | |||
MDR 143oC, TS1, min | 12 | 10 | 9 |
TC90,min | 26 | 22 | 20 |
Mechanical properties | |||
100% Modulus, MPa | 2.6 | 2.2 | 2.4 |
300% Modulus, MPa | 9.3 | 9.4 | 9.8 |
Tensile, MPa | 17 | 15.5 | 16.2 |
Elongation, % | 488 | 422 | 447 |
Standard deviation | 6 | 22 | 7 |
Tear Die C, kN/mm | 66 | 51 | 68 |
Standard deviation | 7 | 23 | 5 |
Abrasion loss, mm3 | 84 | 126 | 78 |
Heat Build Up 30 Hz, 1 MPa static load | 114 | 124 | 115 |
The promoter can be an effective means for reducing the viscosity, improving the properties and decreasing the standard deviation of macro-composite. Thus, GTR/promoter addition requires minor change in formulation, preferably using aromatic oil (RAE). The new solution allows using up to 20 phr of GTR into the premium rubber compound. Experiments show that active filler added while mixing forms the new network in devulcanising volume and can suppress a sulfide network scission. Therefore, rubber processing requires an innovative approach to retain initial elastomer structure.
The Main Results of this Work are the following:
The two compounding tools cancel the rubber reclaiming stage prior to mixing with virgin rubber that decreases operational and composition expenses. In addition, these tools allow using a greater ratio of GTR for the virgin elastomer for similar performance retention. New tools offer broad approaches to tyre recycling by variation of the ratio of GTR due to a new compounding tool and modifier/coupling agent use. Tyrec process is easily integrated into the rubber compounding process and uses standard industry equipment.
The compounding tools work well with the existing mixing equipment. This piece of technology will meet targest without reinventing the composition where GTR is used. The process prevents rubber decomposition and inhibits malodourous gas release, further allowing production with reduced energy consumption. The TyreElast has an original rubber smell. The developed compounding tool decreases operational and compound expenses.
References
1.V. Herrmann, A. Heinrich, Influence of ground truck tires as an additive on the properties of a truck tread compound, Int. Polymer Sci and Techn, 2017, 44, No. 2, 2017,
- Mizuno, N.; Misono, M. Heteropolyacid catalysts. Curr. Opin. Solid State Mater. Sci. 1997, 2, 84–89.
- G Maayan, R Popovitz-Biro, R Neumann, Micelle Directed Synthesis of Polyoxometalate Nanoparticles and Their Improved Catalytic Activity for the Aerobic Oxidation of Sulfides, J. Am. Chem. Soc. 2006, 128, 4968-4969.
- S.Kawahara, Y.Yamamoto, Y.Isono, Volume, interface and cavitation effect on the properties of macro-composites, J. Soc. Rheology, 2014, v 42, No2, 79-88.
- D. J. Burlett, J. T. Lindt, Reactive Processing of Rubbers. RCT, 1993, Vol. 66, No. 3, pp. 411-434
Author: Dr. Moshe Rakhman, Tyrec senior chemist, specializes in the closing the loop: re-use of thermoset rubber , thermoplastic elastomer. Dr. Rakhman is the author of technical papers and patents. rakhman@tyrec.com