Australia is one of the world’s largest consumers of OTR tyres, yet its OTR recycling record is poor; TSA’s latest report looks at the issue in detail
Traditionally, mining operations would make use of the excavated areas when work had finished to dump their waste. In some places, the sites would become mixed waste dumps. It makes sense that the cheapest route to dispose of waste is to bury it. There are minimal transport costs, no processing costs, and the site is ready for use without any modification.
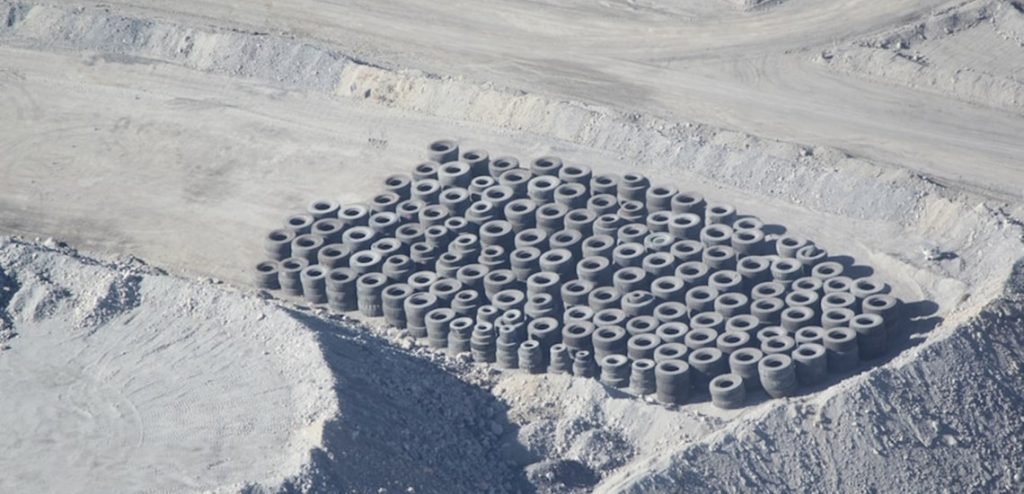
However, simply landfilling waste, especially tyres, is no longer morally acceptable in most developed economies. So, surely Australia cannot simply allow landfilling of OTR tyres to continue? But it does, and that is a problem that Tyre Stewardship Australia say needs to be addressed.
OTR tyres contain a high level of natural rubber, and companies such as Michelin and Kal Tire, amongst others, have recognised this. When driven by legislation in Chile, these companies developed processes to recycle OTR tyres.
Essentially, the Chilean government made it more economical to process the tyres for recycling than to bury them. That simple move through legislation mandating recycling changed the way tyres were handled in the country.
Tyre Stewardship Australia’s report called “Tipping the Balance” identified five key barriers to OTR tyre recycling:
- the low perceived costs of on-site disposal,
- the high costs of logistics and recovery,
- uncertainty about technologies and waste management approaches,
- uncertainty about end market size and capacity, and
- a low priority for tyre waste stewardship.
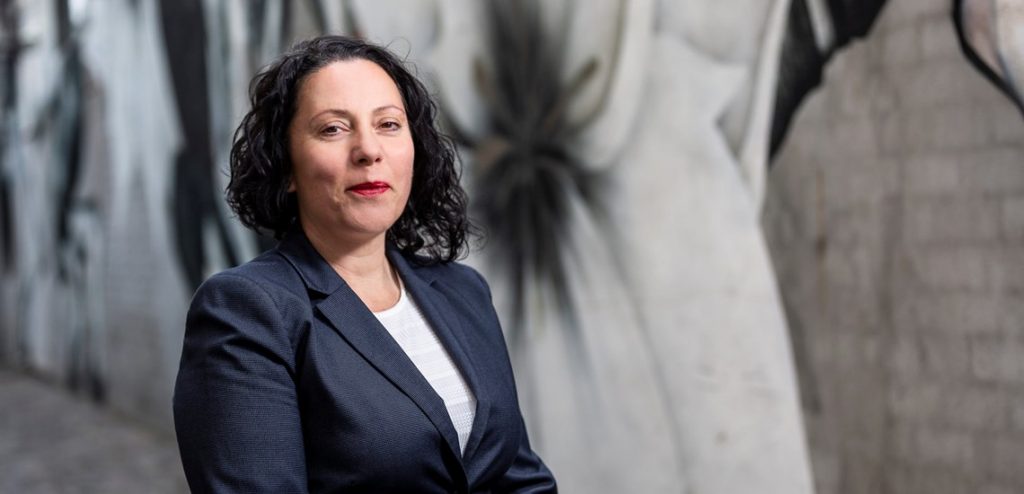
TSA’s Lina Goodman says; “Our first step is to reconsider the current voluntary Tyre Product Stewardship Scheme; at the moment, we don’t have the authorisation to support the supply chain for OTR rubber products that Australia needs.
“A second step is to engage all the parties involved in supplying, using, and recovering OTR rubber products and the various other stakeholders who are affected by or have a say in how these products are used.
“I’m talking about tyre manufacturers, wholesalers and recyclers, mining and agricultural companies, governments at all levels, researchers, indigenous peoples and local communities. I encourage them all to read this report and understand the implications and opportunities it identifies. Ignoring this report and failing to act will only compound the existing issues and exacerbate this already lost opportunity.”
Goodman is clearly pulling her punches. There is a political game being played out on tyre stewardship in Australia, where the voluntary nature of the system allows massive loopholes in management. However, changing this will take a change of culture in government against what is a very powerful lobby in the country, the mining industry.
It is easy for Tyre and Rubber Recycling to make suggestions from afar, and as always, those at the business end of the industry will have all the arguments as to why there are barriers and why they cannot be overcome.
Of course, we only need to consider how Europe changed its waste tyre challenge. It outlawed the landfilling of whole tyres (with derogations), Or to Chile, where the law was created to drive recycling forward.
If the Australian government were to make Tyre Stewardship Australia mandatory, and if they introduced federal legislation that prohibited the landfilling of OTR tyres incrementally, as has been done in Chile, then the issue of recycling OTR tyres would get addressed pretty quickly.
Then there is the potential to question the sustainability credentials of the tyre manufacturers themselves. The tyre industry media is full of stories of tyre manufacturing sustainability, which Tyre and Rubber Recycling has questioned in the past. So, if these manufacturers are so keen on sustainability, why are they allowing their products to be landfilled? They are the producers of the product, and internationally, producer responsibility has been taken as going back to the manufacturer. Why are these companies allowing their products to be landfilled? Why are they not helping to create a sustainable recycling process for OTR tyres?
Is tyre manufacturer sustainability only a reality as far as it is driven by legislation?
So far, we have discussed the first and last barriers – the ease of landfill and the ineffectiveness of a voluntary stewardship scheme.
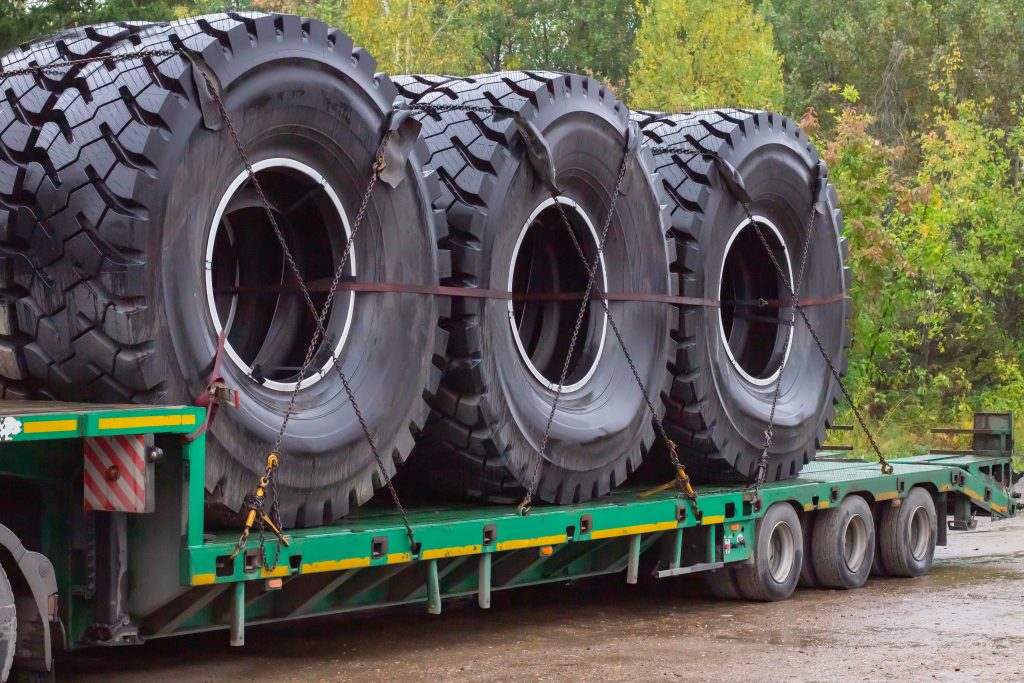
Reverse logistics can address the costs of logistics and recovery. If a supplier delivers a set of tyres to a mine – his trucks have the capability to take away the arisings on their return journey. The issue then becomes one of how to process those tyres. The lead on that has been taken by retreading and by recycling. OTR tyres can be retreaded for a second use, and the plants being developed by Michelin and Kal Tire, and others show that the OTR tyres can be processed to recover steel, oil and carbon black, at least. Rubber buffings from OTR tyres are high in natural rubber, and there is always a demand for reclaimed natural rubber products.
The technologies are available to buff, cut, pyrolyse, and devulcanise – the question becomes a matter of economics and choice.
Of course, as always, the final piece of the jigsaw will always be the markets – and as with all other recycled tyre materials, what do you do with the recovered materials?
Well, rubber crumb with a high natural rubber content is, anecdotally, always in demand; tyre-derived oil and recovered carbon black are in growing demand globally, – and here we can look to the carbon black producers as an indicator of the change in the market. All carbon black producers of any note now include sustainable blacks, either incorporating recovered carbon blacks or using sustainable carbon black manufactured from tyre-derived oil.
From the outside, the argument is clear that Australia’s OTR tyres should be recycled rather than landfilled. But politics and economics always cloud the picture and obfuscate the arguments. However, ultimately, Australia will have to act on its OTR tyre arisings and address the issue of landfilling once and for all.
The Tipping the Balance report is available here.