Since it was founded in 1962, Maris, an Italian manufacturer of co-rotating twin-screw extruders, has claimed one of the leading positions in the research of new state-of-the-art applications for its products.
Devulcanisation Technology
With the aim of providing its customers with the widest range of choices, every mechanical component of Maris’ extruders is entirely in-house manufactured. Maris says that it is one of the few companies in the world able to customise its co-rotating twin-screw extruders according to its customers’ specific needs and this is true also when it comes to rubber devulcanisation.
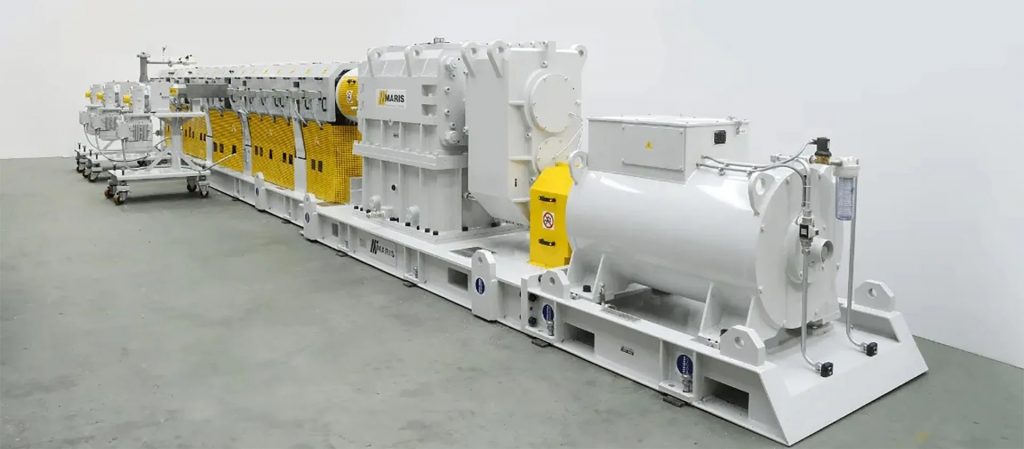
Rubber devulcanisation is a selective breaking process of an elastomer S-S and C-S bonds, which produces only a limited degradation of the polymeric structure (C-C bond).
Different methods to obtain a devulcanised product are known and may be physical (ultrasound, microwaves, and mechanical stress), chemical (the use of devulcanisation additives) and synergistic (thermo-mechanical, thermo-chemical).
Maris, who have been active in the rubber devulcanisation and extrusion field for more than 10 years now, has developed a patented thermo-mechanical synergic process – without the use of chemical additives – that has been used on a large industrial scale and which involves the rubber transition from an elastomeric cross-linked system (vulcanised rubber) to a plastic non-cross-linked system (devulcanised rubber).
The thermo-mechanical devulcanisation is possible as S-S, C-S and C-C bonds have different characteristics; a significant difference in terms of elastic bonding constant (kcc≈100> kcs> Kss≈3) and a different bonding energy (respectively 270, 310, 370 kJ / mol). Thanks to the appropriate combination of and mechanical thermal energy, it is possible to selectively break the S-S and C-S bonds.
Maris devulcanisation process allows working with the following types of rubbers:
- ELTs – End-of-Life Tyres
- Car tyres
- Truck tyres
- Off road tyres
- ACM – Polyacrilic Rubber
- BR – Butadiene Rubber
- EPDM – Ethylene Propylene Diene Monomer
- FKM – Fluorelastomers
- IIR – Butyl Rubber
- IR – Isoprenic Rubber
- NR – Natural Rubber
- Q – Siliconic Rubber
- SBR – Styrene Butadiene Rubber
Chemical and rheological analysis carried out on devulcanised material, have shown that – through this process – a devulcanisation yield of 60-80% can be obtained.
Furthermore, it is claimed to be possible to re-use – in general – from 15 to 50% of the devulcanised material for the same application of origin and, according to the material final use, it is possible to increase the percentage of devulcanised material of the final compound (over 50%).
In terms of mechanical properties of the final compound, Table 1 compares the mechanical properties of an IR-based vulcanised compound (100% virgin) and a vulcanised compound containing 40% of devulcanised IR, both used for the same application and vulcanised in the same way.
Parameters | IR: Virgin | IR: Devulc.(40%) + Virgin(60%) |
Modulus at 100% (M Pa) | 0.95 | 0.90 |
Modulus at 300% (M Pa) | 1.78 | 1.75 |
Tensile strength (M Pa) | 22.91 | 19.94 |
Elongation at break (%) | 891 | 835 |
IRHD Hardness | 67.1 | 62.2 |
Elastic Yield | 48.4 | 42.8 |
Comparison of mechanical properties of an IR-based vulcanised compound (100% virgin) and a vulcanised compound containing 40% of devulcanised IR, both used for the same application and vulcanised in the same way.
The table shows that potential losses of the devulcanised virgin system – in terms of mechanical properties – are negligible and comparable to the non-devulcanised virgin product by further confirming the effectiveness of this thermo-mechanical process within the field of rubber devulcanisation.
Devulcanisation therefore allows an effective use of vulcanised rubber waste and the possibility to obtain a second raw material by reducing the costs and the consumption of virgin material.
Layout of an extruder for devulcanization.
C-TSE size (mm) | 20 | 30 | 40 | 50 | 58 | 70 | 80 | 92 | 112 | 133 |
Output (kg/h) | 5 10 | 20 30 | 50 80 | 80 100 | 100 150 | 150 250 | 150 350 | 400 500 | 550 650 | 700 800 |
At Maris Technological Centre, it is possible to carry out devulcanisation tests in order to verify the effectiveness of the process.