Rubberised asphalt, or rubber-modified bitumen, is not a new process. However, there are many different approaches to the end product – one conference in the USA had 24 presentations, of which 23 were about variations on rubberised asphalt
It started being used in road surfacing in the 1960s and has been adopted around the world by various states as a certified road construction material. However, its use has often been limited to specific projects, such as airport approach roads or test stretches of roadway.
When it does get used in a local project, it is newsworthy. However, the mere fact that rubberised asphalt is newsworthy suggests that it is far from the norm. Why is that?
In this article, we speak with some leading experts in rubberised asphalt, Serji Amirkhanian from the USA, Brian Kent from the UK’s Tarmac, and Luis Alfonso de Leon, who has experience with rubberised asphalt in Spain, perhaps the most developed market in Europe. We ask the question, why has rubberised asphalt not been more widely used?
Amirkhanian explained that there are two rubberised asphalt types – dry mix and wet mix. Dry mix sees larger rubber particles used to coat the aggregate being used, and the reaction takes place between the rubber and the bitumen as the asphalt is laid. The wet process sees finer rubber compounds added to the bitumen in the production stage. The wet method is the more commonly used technology both in the USA and in Europe.
The only difference is the way the rubber is added
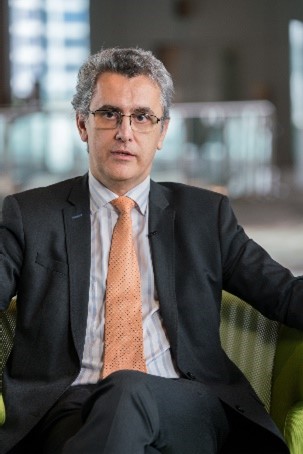
Luis Alfonso de Leon repeats that explanation but adds that the end product is essentially the same, whichever process is used. The only difference is the way the rubber is added. We want to produce a rubberised asphalt mix with better properties than the standard mix, perhaps even compared to polymer-modified asphalt.
“If we focus on the asphalt as the end product that we lay. We can improve the properties by the addition of a polymer modifier or rubber in either process. When we add rubber to the asphalt, we can reach similar properties to polymer-modified asphalt, sometimes a little lower, sometimes a little better. The key question here is that we use a more sustainable material when using rubber. Polymer-modified binder uses artificial or chemical additives that are not sustainable at all.
“The other point is an economic one. The price of polymers is linked to oil, which is volatile and higher than the cost of rubber from ELT. Therefore, there is no price stability in polymer-modified bitumen. However, rubber-modified bitumen comes from a very stable feedstock from ELT. Therefore, using rubberised asphalt, we can give stable prices, and we can better predict the costs involved. This is a huge advantage for the users of modified bitumen as they have stability in costs. So, on economic, technical and sustainability aspects, rubber-modified asphalt is a better prospect when compared to polymer-modified bitumen.”
The advantage of rubberised asphalt over traditional bitumen asphalt is that it quite simply lasts longer; this results in fewer road repairs being required. However, it is also more flexible, so it can absorb slight deformations and is less prone to cracking due to expansion in extremes of climate. All these points are positive, but in today’s market, some local authorities are looking at another quality of rubberised asphalt: its ability to dampen noise. Some reports suggest a 3dB reduction in bypass noise.
These advantages for rubberised asphalt can make it a bit of a “no-brainer” for the technicians with a positive approach to new technologies. Though, rubberised asphalt is not really a new technology, just one that has been slow to be adopted.
Rubber increases the useful life of the pavement
De Leon summarised the key benefits; “When we use rubber, we increase the useful life of the pavement. The mix is more sustainable and has a better lifetime cost due to less maintenance. It resists cracking and deformation of the pavement against rutting, and it reduces the “fatigue” of the road surface. Another helpful point is that rubberised asphalt helps reduce road noise for users and local residents. And, of course, using rubberised asphalt reduces the tyres that get stockpiled.
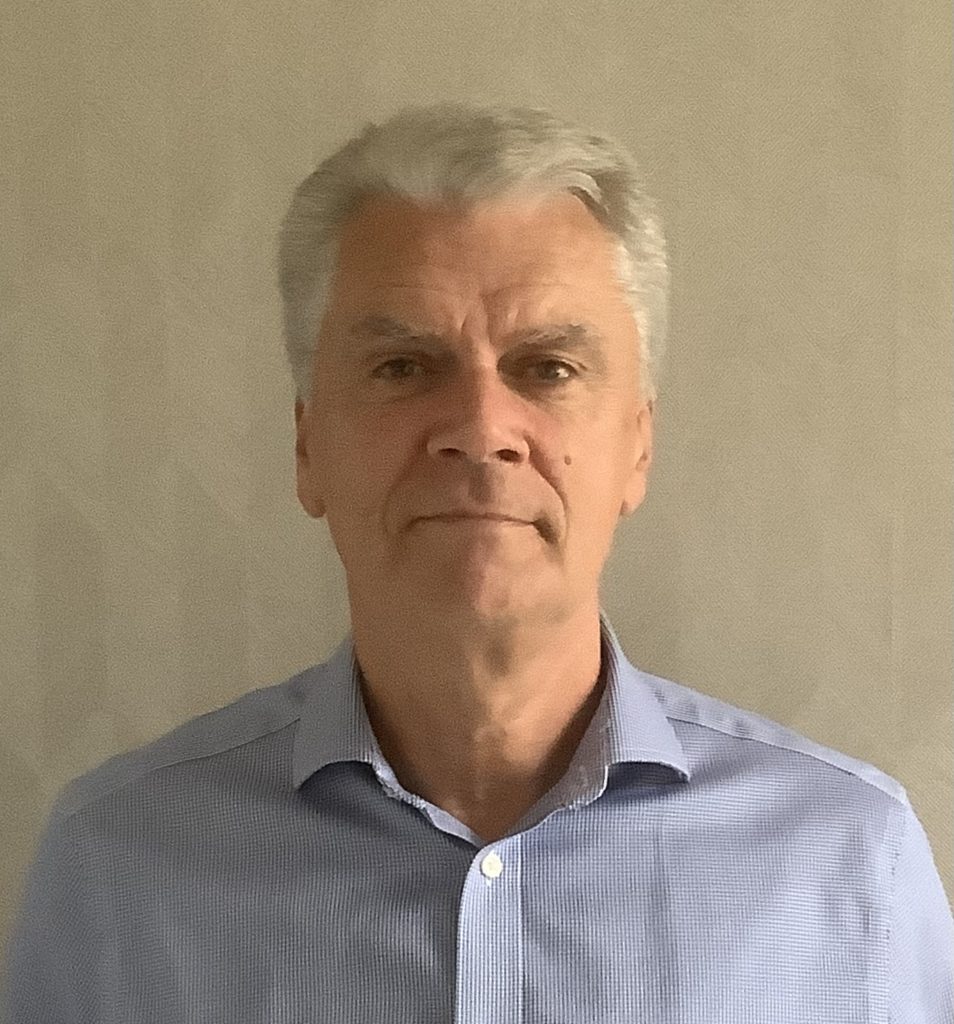
Tarmac’s Brian Kent explained how Tarmac became involved with rubberised asphalt; “We started looking at rubberised asphalt back in 2011 when the landfill ban came into effect. So, we thought that we might be able to do something with tyre rubber.
“There are two types of bitumen used in the UK, straight bitumen, and polymer-modified bitumen. In some parts of the world, they used rubber-modified bitumen to make asphalt. So, we started looking at rubber as an option for polymer-modified material. At that stage, we were putting around 0.6 – 0.7 per cent rubber into the mix, around one tyre per ton of asphalt.”
Kent explained that only the tyre walls were used by Tarmac, and that the material came in a 0.5mm crumb from a large UK processor. “However,” explained Kent, “in 2019, Highways England became interested, and they wanted to put more rubber into the roads. So, we increased the rubber content to 1 per cent on that product and supplied that to Highways England on the M1 in Leicestershire.”
Kent is keen to use as many tyres as he can in rubberised asphalt. He explains, though; “We can add rubber to bitumen and get a lower grade polymer modified mix. It is not as good as polymer-modified bitumen, but it is better than straight-run bitumen. It is a win-win: we use tyres and improve pavement performance.”
No wet-mix capacity in the UK
Asked about the process, Kent told Tyre and Rubber Recycling that in the UK, they had to use the dry mix method. “We use the dry process because the wet process does not exist in the UK. No plants are producing wet process rubberised bitumen. When we spoke to Shell and other providers, they advised that it was very expensive to shear rubber into bitumen. So, no one does this in the UK, and we went down the dry route process.
“The fine-milled crumb, around 0.5mm, is added with the dust and the aggregate at the mixing plant at the same time as the bitumen is added. The wet, or shear process sees the refinery shearing the powder and adding it to the bitumen at the point of manufacture.”
On the use of rubber De Leon had a different take. “We can expect to use between 2,000 and 4,000 tyres per 5cm depth per kilometre of asphalt laid.” Interestingly, De Leon added; “Normally, it doesn’t matter what is used. At TRS SA, we separate tread and sidewall into different materials, but it doesn’t make any difference in the asphalt. However, truck tyres are better for asphalt because they have a higher natural rubber content, whilst car tyres have a high silica content. At the end of the day, both of them work.”
The downside to rubberised asphalt is that there have been issues with the technology used to lay the material. Still, those have been overcome, so what is the one significant disadvantage? It is, at the point of delivery, more expensive than conventional asphalt mixes. However, its longevity and Life Cycle Costs are much lower than traditional practices. That longevity may actually be the biggest disadvantage that rubberised asphalt has.
Amirkhanian explains; “The road builder lays a road and knows that he will have to go back and repair or relay that road in, say, five to ten years. If he lays a road lasting 15 – 20 years, he thinks that he has reduced his future business.”
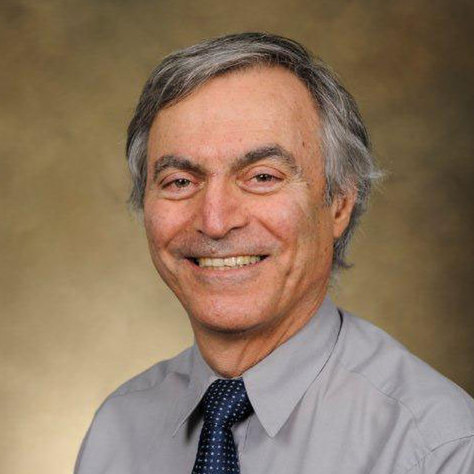
Perception of loss of future work is an issue
Amirkhanian tells of a project in Asia, a bridge on a heavily trafficked road that saw the roadway surface needing repairs or relaying in months rather than years. The authorities wanted to see what rubberised asphalt could do. So, they asked him to oversee a rubberised asphalt project on a bridge that would be used as a trial section. The contractors said that if it lasted three months, it was as good as they already used; if it lasted six months, that would be excellent. If it lasted for a year, he would be a hero. Eight years later, the rubberised asphalt surface has needed no repairs. However, highlighting the problem the technology faces; despite the success of the trial, not one square metre further has been laid. None of the road contractors want to do themselves out of future work.
Asked about the mileage laid in the UK, Kent replied, “Not as much as we would like. We find that cost is the barrier. There is the cost of collection, processing, and transport of the rubber and that all adds to the cost that we have to recover from the clients. At this time, budgetary constraints are a barrier to the market.”
Aside from the cost, there might be other barriers to the market development, and here Kent highlighted one issue that the onlooker may not have considered. “There should not be any barriers to developing the market. The product is BBA HAPAS approved as Clause 942 material for use on roads. If we want to put any material onto the strategic network, it has to go through that third-party accreditation. So, we are disappointed that we don’t supply more of the material to the market.”
The weak point in the market appears then to be the lack of specification when seeking tenders, but Kent explained that it wasn’t as simple as not setting the specification. “The authorities have to outline their tender process in such a way that they can receive multiple applications,” says Kent. “They cannot specify requirements that only one supplier can meet. Since Tarmac is, essentially, the only player in the market, they have to set their specifications so that other companies can also tender for the work.”
De Leon explained that he had seen a change in the market in favour of rubberised asphalt. “In Spain, there is a mandate to use rubberised asphalt, and local municipalities are increasingly specifying the use of rubberised asphalt. So, we have gone from the product being experimental and “first use” to something that can be seen to be working, making accepting the material much easier for the local authorities and road-makers.
“The door is now open, and the authorities ask us how to implement the technology. They then are putting rubberised asphalt into the specifications; sometimes as a recommendation, sometimes they mandate its use.”
So how does the rubber sector open up the market? How can the industry get rubberised asphalt more widely accepted? De Leon responded: “We must provide the tools and the information to help them make the decision. We need to go to the asphalt manufacturers and help them make the right decisions in creating rubberised asphalt. We must also go to all the stakeholders with very clear information. We need to take away the perception of risk. If we do that, if we can show the market how to include rubber in asphalt successfully, then there will be a change. That change is coming, slowly but always in the right direction now.”