Gradeall, a market leader in waste tyre management, is taking significant strides in the industry with their latest developments the OTR Splitter and OTR Sidewall Cutter
Best known for their renowned MK2 tyre baler and sidewall cutter machines, Gradeall is now addressing the challenges posed by massive Off-The-Road (OTR) tyres.
For years, these enormous tyres have been a significant challenge in waste management due to their size, weight, and difficulty in disposal. However, Gradeall is providing a much-needed solution. Conor Murphy, Director from Gradeall, proudly shares; “These machines are the result of five years of dedicated research and development. We have created a reliable, user-friendly method to downsize these large tyres, responding to the demands of our customers and enhancing our existing tyre recycling range.”
The latest iterations of these OTR machines can now deal with tyres up to 2.2m in outside diameter and up to 1m in width which covers the majority of commonly used OTR tyres.
The OTR Tyre Processing Journey
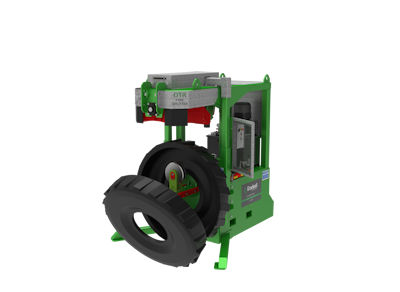
The first step in this process involves the OTR Splitter. Tyres are placed on a precision-engineered, toughened steel idler wheel, which hydraulically lifts the tyre into a rotating cutting blade. This blade, also powered by hydraulics, makes multiple passes around the tyre’s circumference, splitting it in half within approximately one minute. The resulting halves are easily removed from the machine using a forklift.
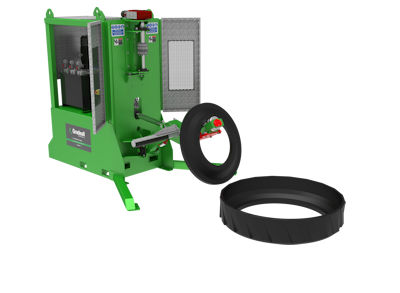
These tyre halves are then moved to the OTR Sidewall Cutter, an enhanced version of Gradeall’s well-regarded Truck & Agricultural tyre sidewall cutter. The hydraulic arm lifts the tyre to a cutting wheel that separates the sidewall from the tread, taking about a minute per tyre half. This process results in each tyre being cut into four manageable pieces: two sidewalls and two tread sections.
By processing OTR tyres through these machines, over 50 per cent of the original space required for storage and transport is saved, drastically reducing costs. The processed tyres are also easier to handle and are primed for further recycling methods such as baling or shredding, turning what was once a logistical nightmare into a manageable process.
Efficiency, Space, and Cost Savings
Gradeall has successfully exported these machines to over 12 countries, and customer feedback has been overwhelmingly positive. Clients appreciate the effectiveness of these machines in solving a previously insurmountable problem, reinforcing Gradeall’s commitment to continuous innovation and improvement.