The United Arab Emirates has long supported industrialisation; Emirati businessmen always aim to be entrepreneurs in different Industrial fields
In 2004, the first attempt in the field of rubber recycling was started by the “National Rubber Factory”, which is still operating today. Then the government in Abu Dhabi founded “Abu Dhabi Waste Management Centre”, to organise the waste management business for the private sector.
In the beginning, the tyre recycling business faced a challenge to find buyers for its products, and then the consumers began to accept rubber tiles and floors in sports, gymnastics and children’s’ areas. In 2015, local cement factories started to use recycled rubber as an alternative fuel, due to its high calorific value. Also, cement factories in Pakistan started to buy recycled rubber from UAE to use as fuel, and the demand continued to increase. Accordingly, a new business of trading in waste tyres was created, and a new profession called “Waste Tyre Dealers”. A price was established for the used tyres and increased over time to the extent of five times the initial value. This resulted in the tyre recycling factories relying on Waste Tyre Dealers rather than collecting by themselves.
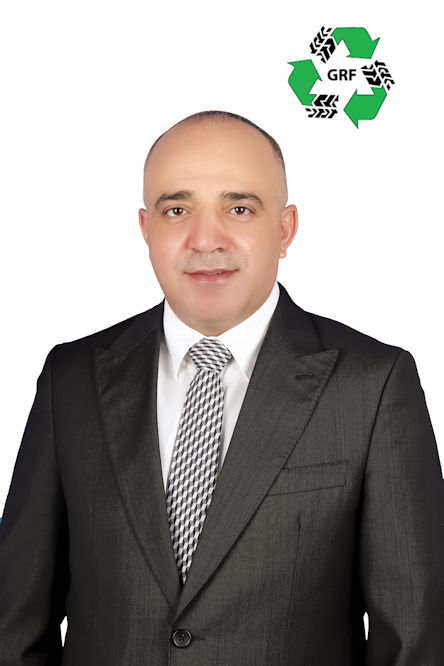
The Gulf Rubber Factory started in 2012, in the Alain area, over a footprint of forty thousand square metres, the location was chosen to be near the waste tyre cemetery, according to Mr. Zaid Albdour, the General Manager of the factory. The production area is a covered area of twenty-four thousand square metres, the rest is stores and managerial buildings and a non-covered area.
The machinery line is divided into two phases, the first is the recycling phase, where the waste tyres are shredded, the wires are separated, and rubber granules are produced to five millimeters. All the phase one machinery is from European origin. Zaid clarified that the initial vision of the board of directors, was to produce a high-quality product. The machinery can recycle in excess of 24,000 tons a year and operates at around 120 tons per day.
The second phase is the rubber production phase, and the machinery is from both Europe and India. Here the rubber granules are ground, before being delivered to the mixing mill. There is a control panel controlling some machines, others are being controlled by a computer programme. Zaid Albdour explained that UAE legislation approves duty exemption for importing machinery in general, but there is no special exemption for the waste recycling field.
When asked about the additives during the production process, Zaid mentioned that, of course, there are additives like natural rubber, oil and binders; all additives were imported, except the binder, which was produced locally.
“The first phase of the production process is almost automated, so we have only nine technicians in that phase,” added Zaid. “While thirty technicians operate the second phase, in addition to administrative staff and drivers.”
Some of the technicians are qualified as they operate modern machines, others are only for carrying and handling, Gulf Rubber Factory trains its technicians in-house, whilst the technicians responsible for the Security and Safety are trained at the Emirati Security Defense administration.
On the question of the energy used to operate the machines, Zaid said that they used electric drives on all machines, and many of the machines are designed to save energy. He added that their tyre recycling technology is environmentally friendly, the company did not produce any hazardous material nor material that needed treatment.
Tyre and Rubber Recycling asked about Gulf Rubber Factory products, he answered we produce cattle corrals, gym flooring and shock absorbers, sports floor underlay, ballistic tiles and blocks, pipe support inserts, pads, sound control underlay and floating floors, rubber mulch and granules.
Zaid Albdour stated that mass production, high quality and delivery on time are their main strengths, because of the latter, the Gulf Rubber Factory managed to export around fifty per cent of the production to other Gulf countries like Saudi, Qatar, Kuwait and Oman.
Lately and due to the increase in the cost of waste tyres, they had only been able to export ten per cent of the production. So, the price of waste tyres is the major challenge facing Gulf Rubber, said Zaid. “Moreover, we face competition from the imported final products, those products do not have the same level of quality as our products, but we addressed the government to establish standards for the characteristics of the imported products. That is an important strategy that should be adopted by the Government, to support local industry.” Zaid added that there is a support program for industrialism in general, but nothing specific for recycling rubber factories, also there is no support from the Ministry of Environment.
Zaid explained that they started building the factory in 2009. In 2012 they started the tyre recycling phase producing rubber granules; in 2014 they started the rubber compounding to produce the floor mats. In 2017, they developed the technology for floors for gymnastic playgrounds and shooting fields, but the latest development came in 2020 when the factory introduced the sound insulation material used between the floors of large buildings.
In conclusion, Tyre and Rubber Recycling asked Zaid Albdour about the company’s influence on the tyre recycling industry? He mentioned that their factory has an impressive imprint on the industry, from protecting the environment to disposing of many used tyres, additionally creating goods that were previously imported into the market and providing more job opportunities. “We are special,” added Zaid, “in both combining tyre recycling with the rubber industry. If I were to go back to the beginning, I would do this all over again. Even the second generation of proprietors is receiving knowledge and expertise from us in the plant. We strongly foresee that the demand for recycled rubber will increase as long as cement companies keep using it as fuel.
“Our long-term goal is ‘to maintain improving the product’ quality and diversity while stepping up our marketing and export initiatives.”