At the Siemens Tire Day: Accelerate the Future Tire Industry event, in Chennai, Siemens exclusively introduced ReTyre’s tyre recycling technology to leading tyre manufacturers
On the 10th May 2024: UK-based ReTyre, presented its technology and proposition to the Indian tyre manufacturers who have strict Extended Producer Responsibility requirements to meet.
The ReTyre technology will maximise the use of “green” materials and enable them to maximise the incorporation of activR in their production process, saving on costs, and lowering carbon footprints through recycling at the source of the waste.
The event was attended by high ranking R&D representatives from Apollo Tyres, CEAT, Continental Tyres, TVS Tyres, Goodyear, Deloitte, Yokohama who were introduced to the output from Re-Tyre’s UHP (FDPT® by ReTyre) water jet micronisation process.
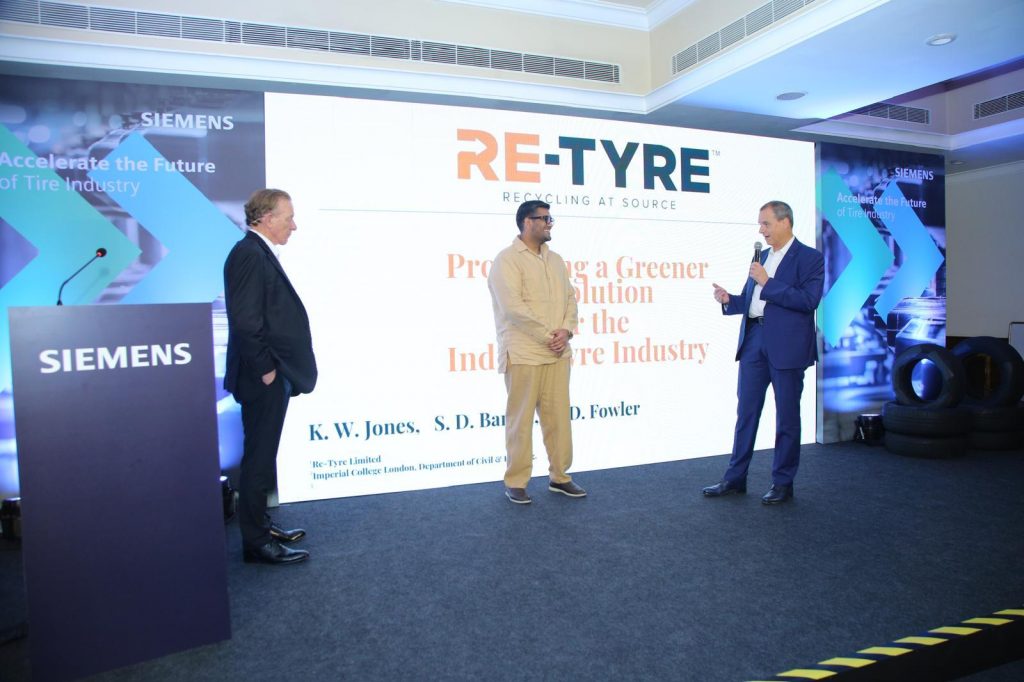
The ReTyre process takes car tyres and separates the rubber content from the belting and beadwire by using a water-jetting process called FDPT®. The process leaves a recyclable steel and a partially devulcanised rubber, which ReTyre call activR.
The process leaves zero waste and is contained in a shipping container needing minimal infrastructure or logistics resources, just the power source and a reservoir of recirculated water.
activR has, as the name suggests, an active surface, which has been partially devulcanised by the process, making it eminently suitable for inclusion in new tyre and rubber products.
Mr. Shravan Bansal, a co-founder of the company, said: “We would like to first introduce this technology to all tyre manufacturers for their factory rejects as they can optimise the final produce according to their desired composition.”
The technology has been developed by ReTyre in the United Kingdom after stringent research of 15-plus years at the Imperial College London.
The founder of ReTyre, Mr. Shravan Bansal, has set an ambitious target to commence the mass production of the machine in India with a vision to make India the first country to turn what is considered a Linear Industry into Circular Industry by cutting down PCR tyre scrap into 100 per cent sustainable materials.