Poland’s Contec is moving quickly towards becoming a key player in the tyre pyrolysis sector. 2023 has seen the company receive 15 million euros of investment, enabling the company to work towards its upscaling goals
However, CEO Krzysztof Wróblewski has a longer-term view of where Contec is heading and in a third interview with Wróblewski, he outlined the latest developments at Contec and plans for the future.
The first stage in the development of Contec is the expansion of its plants across Europe. Wróblewski says; “The most important message is that we have been successful with fundraising. The 15 million euros funding that we have just completed will allow us to expand the Szczecin plant. The plant is already operational. We have two lines functioning well, and we want to add another two lines.
“The second step is to find the right partner to help us scout for new plots for further expansion. We already have an agreement with one of the best providers of this service in Europe, we just need to sign the deal. We will be looking for the best plots, and we will be scouting different regions. We will be looking at Southern and Eastern Europe, but also in other markets.
“We want to do this in a strategic and structured way, assessing the criteria that are important to us, considering all the regions and sites with the same criteria to find the best place for us to grow.”
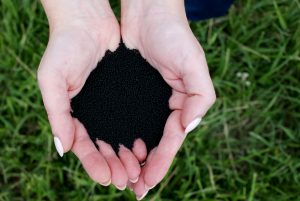
One of the issues with tyre recycling is always the transportation of the raw materials. Shipping tyres is inefficient, the bulk of the space taken in a truck carrying tyres is just air unless the tyres are baled. However, the more effort put into the feedstock, the greater the cost. So, Contec is seeking to locate new plants in areas close to tyre arisings. This is more likely to be in countries or regions with currently poorer recovery rates, often in Eastern Europe.
“The feedstock location is one of the most important criteria. It is not easy to transport huge quantities of tyres. So, we are looking for locations where there are large volumes of tyres with no established chemical or mechanical recycling. We will be looking for markets where they have not yet solved all the issues of tyre recycling, and there is an opportunity to help in addressing the issue of end-of-life tyres.”
Wróblewski continues; “The second criterion is the access to a workforce. Everyone is facing challenges in finding the right employees for the sector, so we need to identify markets where we can access qualified personnel and all the auxiliary companies that need to be there to support our operation. When we build a plant, we need to be sure that it will be operated properly.”
In some ways, these two points are basic steps, but Wreblówski then talks about the third criterion, and here the context gets a little complicated as it involves legislation. “The next question is how we meet the legislation around recycling and its harmonisation in the EU. Unfortunately, in different countries, we have different criteria and different rules around end-of-waste. It is extremely important that we can achieve an end-of-waste status for our output. We have gained this in Poland where we have a product, and we want to have the same in all our plants. There seems to be no point in creating an output that is still considered a waste. It is an especially important criteria for us that we can produce an end product that is not labelled as waste.”
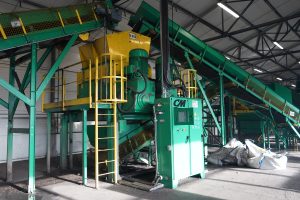
It is clear that recovered carbon black is easy to transport, but if that transport requires additional licences, paperwork, and costs, that then detracts from the viability of the project.
Wróblewski adds; “We are not the experts in tracing sites and dealing with planning and licences, which is why we have decided to take the strategic approach of using a specialist in that area.”
Hand in hand with planned growth will always be a need for research and development. Tyre and Rubber Recycling asked Wrobleski where Contec was heading with future R&D projects.
“Contec has a very broad view on R&D,” said Wróblewski. “We have over 30 R&D projects through to 2027. These have different levels of complexity and are at various levels of advancement. I would say that these projects are in diverse groups – in application R&D mostly focused on rcb in rubber and other applications. So, we will develop our expertise in different applications, even in the tyre industry, the application in the sidewall will differ from the application in the tread, for example, but also in other non-rubber uses.
“The second part of our R&D is in product development itself. Here we want to make what we produce better in the case of certain applications, I can’t give details yet, but it could bring the value of the rcb to a higher level by a considerable amount due to the specific characteristics that we can achieve with our rcb in certain applications.
“Because we are technology developers, some part of our R&D will be in developing the technology for different feedstocks such as plastics or biomass, or other feedstocks that can be chemically treated where our technology can be adapted. This is another area where our R&D can be focussed.
“These are the three pillars of our internal R&D, but we also have external R&D with partners. One in particular is our joint development with the Swiss company TRS spa. They water jet the tread of the tyres, but they are looking for solutions for the sidewalls and the casings. We are conducting a joint R&D project with TRS. They are experts in compounding, and we are taking their sidewalls and looking at solutions based on treating just the sidewalls. This will bring certain qualities to the rcb. This will bring specific qualities as the rcb from the sidewalls will be a lot lower in ash content. This will create a new grade of rcb made from just the sidewall. This should find specific applications as it will be more consistent in quality. We are in the process of developing that, gathering the sidewalls and when we produce this rcb, it will be milled and pelletised in our system and sent back to TRS, who will then test it for its in-rubber performance.